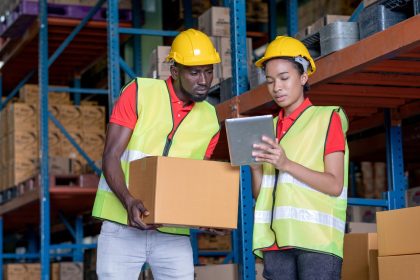
For a customer, the words “shipping delays” can lead to frustration, disappointment, and potentially, a lack of trust in a company.
A delay in receiving goods from a business or supplier can cause a ripple effect in the supply chain. It not only affects the customer but also other areas of the supply chain. But having a well-managed system in place can help prevent, or at least reduce, some of the challenges businesses face with delayed shipping of goods and services. Keep reading!
Common Causes of Shipping Delays
Shipping exceptions are a common occurrence in various industries, including retail, automotive, manufacturing, and commercial services. Oftentimes, these delays can be addressed and/or prevented with proper contingency planning. There are, however, times when businesses are at a standstill and at the mercy of supply chain disruptions. Here are some common causes of shipping delays and exceptions:
Weather-Related Disruptions
Mother Nature is often responsible for many shipping delays, particularly in North America and Europe. Variable weather conditions and natural disasters can halt a shipment of supplies or goods for days or weeks at a time. This is especially common with land deliveries and overseas transportation, even if a business has multiple fulfillment centres across the globe.
Transportation and Logistics Issues
Shipping delays can be directly and indirectly linked to transportation and logistics issues along the supply chain. With rising fuel prices, worker shortages, and an increase in online sales, transportation delays are at an all-time high. Labour-related issues are associated with low pay offerings, sick days, and strikes.
Customs and Regulatory Hurdles
International shipping has been a challenge for many businesses even before the recent global transporting issues. With tougher restrictions, rules, and regulations put in place at most borders around the world, customs clearance for shipments involves long delays.
Supplier and Manufacturing Delays
Supply chain disruptions from the suppliers and/or manufacturers can gravely impact the delivery times as scheduled. In recent years, these disruptions have been linked to conflicts among countries, shipping ports, and, of course, the global pandemic. With a worldwide labour shortage, economists predict supply chains will continue to have interruptions for years to come.
The Impact of Shipping Delays and Exceptions on the Supply Chain
The enormous impact delays and exceptions have on the supply chain cannot be properly measured. On the surface, these disruptions appear to only affect customer service and customer expectations, but behind the scenes, the effect is more profound.
Financial Implications
Financially, shipping delays can cripple a business, particularly if it becomes a reoccurrence within the supply chain. With every delayed shipment, a business can face increased costs in storage and inventory, penalties, returns, administration fees, and expedited shipping. In addition, a loss of revenue from poor customer experiences due to shipping delays can be significant for a business.
Customer Satisfaction and Loyalty
Delays within the supply chain can hurt the customer experience. Shipping delays are the number one complaint from customers who use e-commerce sites. In fact, customers these days expect their products delivered within days, if not hours. Dissatisfied customers may choose to take their business elsewhere, which opens the door for competitors to swoop in and acquire those customers instead.
Reputational Risks
A brand depends on its reputation to continue to survive in a competitive industry. Shipping delays can cause customers to lose trust in a brand, therefore affecting their support and promotion of a brand. By using social media platforms to voice their concerns, customers can create a negative public perception of a brand, which could affect their various partnerships in the business world.
Proactive Strategies to Mitigate Shipping Delays
In an ideal world, there would not be any shipping delays or exceptions along the entire supply chain. But, unfortunately, it’s a reality. To create a near-perfect logistics system, here are some strategies businesses can adopt to mitigate shipping delays:
Diversify Suppliers and Logistics Partners
Effective planning begins with building a resilient network of suppliers and logistic partners. Keeping updated on changing local regulations within the suppliers’ regions can prevent delays along the supply chain, particularly in the delivery sectors. Also, it’s important to work with multiple carriers for customer deliveries since ground, air, and door-to-door options may not be possible in some destinations.
Implement a Contingency Plan
To be successful, shipping departments must have a contingency plan for extreme weather, transportation issues, and other unforeseen incidents. Monitoring deliveries and weather conditions can help businesses create a contingency plan if certain patterns are observed often. This can include developing alternative delivery routes and shipping options. This contingency plan may also involve stockpiling certain items during peak seasons.
Strengthen Communication Channels
As customer satisfaction is one of the most important goals in the business world, having clear communication channels within the supply chain is crucial. Suppliers, carriers, and customers must have access to transparency and open communication to address any potential or existing shipping delays. By having direct interaction, businesses can be prepared with alternatives if deemed necessary to shorten delivery delays.
Invest in Technology
“Successful investing is about managing risk, not avoiding it”. This quote rings true in the e-commerce world when it comes to investing in technology to improve shipping. Real-time inventory software allows all parties involved to be informed via notifications about delivery statuses and/or delays. Technology enhances the customer experience while allowing businesses to monitor shipping through data analytics to identify potential problems.
Be Proactive in Shipping Management with Lean Supply Solutions
Protect your business’s reputation and financial future with Lean Supply Solutions’ supply chain optimization and logistics management services. We offer manufacturing support, consulting, project management, product and order fulfillment, and warehouse and distribution services customized to your needs. Contact us today to get a free quote on how we can help you navigate shipping delays and exceptions in your supply chain.