Lean Supply Solutions Expands Global Footprint with New Distribution Facility in Poland
Lean Supply Solutions (LSS) is a leading provider of end-to-end supply chain solutions, specializing in warehousing, distribution, transportation management, and technology-driven logistics. With a strong reputation for reliability and innovation, LSS supports a diverse portfolio of clients across North America and Europe. Headquartered in Canada, the company currently operates over 1.5 million square feet of strategically located facilities across Canada, the United States, and the United Kingdom, delivering seamless and efficient logistics solutions to some of the world’s top-performing businesses. To learn more, visit www.leansupplysolutions.com.
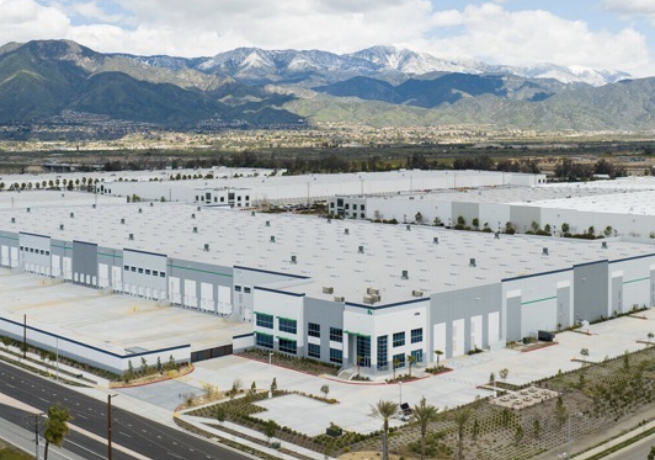
As part of its global growth strategy, LSS is excited to announce a new distribution and warehousing facility near Gdańsk, Poland, scheduled to begin operations in Q1 2026. Gdańsk is a key logistics hub with strong land and sea access, enhancing LSS’s ability to serve European markets more efficiently.
The initial phase of the expansion includes a facility of approximately 20,000 to 30,000 square feet, with plans to double this footprint within the first 12 months of operation to meet anticipated customer demand. This facility will play a central role in LSS’s European fulfillment network, offering scalable warehousing, inventory management, and final-mile distribution services tailored to the needs of current and future clients.
The investment, ranging from $750,000 to $1 million USD, includes facility setup, advanced material handling systems, and technology infrastructure. The expansion is also expected to create 10 to 20 new jobs in the region within the first year, including roles in logistics, operations, and support.
This strategic expansion aligns with Lean Supply Solutions’ vision to provide globally integrated logistics capabilities while maintaining the agility and customer-first approach that defines the company. As supply chains become increasingly complex and globalized, LSS is committed to investing in infrastructure that empowers clients to succeed in dynamic markets. For any inquiries, please email info@leansupplysolutions.com.
- Published in News
Lean Supply Solutions Expands U.S. Presence with New State-of-the-Art Facility in California
Lean Supply Solutions (LSS), a leading provider of end-to-end supply chain services, is
proud to announce the opening of a major new distribution and fulfillment center in Redlands,
California. The facility officially launched operations in October 2024 and represents a
significant milestone in the company’s North American expansion.
Located at 27358 Pioneer Avenue, the new Redlands site spans 460,805 square feet and significantly enhances LSS’s capacity to serve clients across the western United States. With a global logistics network that includes over 1.5 million square feet of space across Canada, the U.S., and the U.K., LSS continues to deliver innovative, technology-driven solutions for sectors including retail, e-commerce, automotive, and manufacturing.
“This new facility underscores our commitment to scalable, intelligent logistics,” said Tom Krzepkowski, President of Lean Supply Solutions. “Redlands is a strategic hub that strengthens our ability to support complex, high-velocity operations in a key region.” The facility New 460 805 sq. ft. Lean Supply Solutions facility in Redlands, California, launched in October 2024.
Lean Supply Solutions Inc – 3130 Caravelle Dr, Mississauga, ON L4V 1K9 features 92 truck-level loading docks, 4 drive-in docks, and a flow-through design ideal for high-volume distribution. Equipped with 70,000 pallet positions and 144 container storage spaces, it is designed for scale and speed.
LSS has integrated cutting-edge technologies at the Redlands site, including autonomous
shuttle trucks, semi-autonomous forklifts, advanced sortation systems, and 2D barcode
and RFID scanning. These tools enable precise inventory control and efficient handling of direct-to-store replenishment, kitting, and complex e-commerce fulfillment.
With this investment, LSS reinforces its position as a forward-thinking supply chain partner equipped to meet the evolving demands of modern logistics.
For more information about Lean Supply Solutions and our services, visit
www.leansupplysolutions.com or contact us at info@leansupplysolutions.com.
- Published in Blog
Mastering Automotive Fulfillment: Integrating Best Practices in Warehousing and Delivery
What makes a supply chain truly excellent? For the automotive industry, it’s the seamless integration of warehousing, fulfillment, and delivery in the USA. Automotive fulfillment involves the end-to-end orchestration of moving vehicles, parts, and accessories from manufacturers and distributors to dealerships, repair shops, and even individual consumers. It includes every step, from receiving goods into the warehouse, managing inventory, and picking/packing, to routing for delivery.
This blog will explore how mastering warehousing and delivery operations can optimize the automotive supply chain and transform your fulfillment process into a powerhouse of efficiency and customer satisfaction.
Warehouse Optimization for Efficient Automotive Fulfillment
Achieving excellence in warehousing lays the groundwork for efficient automotive fulfillment. Here are key areas to focus on.
Strategic Warehouse Design and Layout
Strategic warehouse design is critical. Poorly organized automotive fulfillment warehouses in the USA lead to inefficiencies that have ripple effects throughout the supply chain.
During the planning stages, divide your facility into specific zones for picking, staging, and packing, based on order categories. Next, implement storage systems (e.g., pallet racks, bins) designed to accommodate a range of part sizes, ensuring quick retrieval. Use flow optimization to reduce travel time for workers during both put-away and picking operations. A well-planned layout supports lean operations.
Technology-Driven Warehouse Operations
Technology-driven operations deliver measurable benefits in speed, accuracy, and scalability. A Warehouse Management System (WMS) provides real-time visibility into inventory, enabling efficient order management and accurate stock levels, while barcoding and RFID (Radio Frequency Identification) can provide faster picking, packing, and sorting. Technologies like robotic pickers, conveyor systems, and automated sortation minimize manual labour and boost fulfillment speed.
Make sure to equip warehouse staff with handheld devices for real-time task updates, inventory scans, and error mitigation.
Inventory Management Strategies for Seamless Fulfillment
Inventory accuracy and availability directly impact fulfillment timelines. Demand forecasting is used to ensure sufficient stock is available for anticipated orders. This can help minimize stockouts and delays, which can otherwise cripple the customer experience.
With the vast selection of parts and computerized components, inventory storage needs to support the diversification of different car models. Implement cycle counting and other controls to maintain optimal stock levels and use lot tracking and serial numbers to enable quick responses to recall and enhance customer trust.
Streamlining the Automotive Fulfillment Process
To meet tight delivery schedules and diverse customer needs, your fulfillment process needs to run like clockwork.
- Efficient Order Processing and Management: Fast, accurate order processing sets the fulfillment process in motion. Integrate Order Management Systems with your WMS for synchronized workflows, prioritize orders by urgency or customer specifications, and provide customers with real-time updates on order statuses to build trust.
- Optimized Picking and Packing for Automotive Orders: As automotive parts can be bulky, in kits, or as a single unit, picking and packing strategies need to be varied in an organized and efficient method. Pack items securely to avoid damage and ensure accurate labelling and documentation for smoother shipping and tracking.
- Strategic Outbound Logistics and Transportation Management: Outbound logistics strategies are critical for cost-effective and timely deliveries. Select carriers based on cost-efficiency and the required delivery timeline and always use route optimization tools to minimize transit times and shipping expenses. Develop strategies for managing reverse logistics and returns efficiently, as handling warranties and returns is critical in the automotive industry.
Integrating Warehouse and Fulfillment Technologies
Bridging the gap between warehousing and fulfillment technologies delivers a cohesive, efficient supply chain.
Integrated systems provide organizations with real-time visibility of inventory, orders, and shipping data, enabling data-driven decisions. A transparent system improves decision-making and reduces expenses.
Data analytics, on the other hand, can help businesses identify bottlenecks, improve forecasting, and enhance delivery operations. Accessing purchasing patterns helps you predict your future needs with more accuracy, making your fulfillment operations more proactive and cost-efficient.
The Human Element in Effective Automotive Fulfillment
No level of technological advancement can replace the human element in a well-oiled fulfillment operation.
Specialized Training
To ensure a smooth process, equip your workforce with training that covers the entire fulfillment lifecycle. Training through certification programs, workshops, and refresher courses enhances operational efficiency, while proficiency in real-time operations can lower operating costs by reducing the need to manually check inventory and handle errors. Overall, this ensures employees understand how their roles impact the broader supply chain.
Cross-Functional Collaboration
Within an automotive fulfilment centre, various departments need to work closely together to provide customer satisfaction. This is especially important with warehouse teams and fulfillment/shipping departments. Make sure to foster clear communication and collaboration between warehousing and logistics teams. Regular meetings and shared KPIs can help align teams toward shared goals.
Performance Metrics
Aside from monitoring your team’s efficiency and performance, tracking key performance indicators (KPIs) such as order accuracy, on-time delivery, and customer satisfaction can provide businesses with more details about their supply chain. These metrics help monitor progress and pinpoint areas for improvement.
Best Practices for Customer-Centric Automotive Fulfillment
- Meeting Diverse Customer Needs: No two orders are the same, nor are the needs of each customer. Make sure your customer service caters to different stakeholders and that you offer tailored solutions, for example, expedited shipping for dealerships or warranty options for consumers. Addressing your customers’ diverse needs can enhance the customer experience.
- Expedited Shipping Options and Service Levels: You can achieve excellence in shipping and delivery by providing shipping options that meet different urgency levels. The right fulfillment centres are designed to store and prepare products for safe and efficient shipping. Outsourcing your automotive fulfillment allows you to focus on the service without compromising profits.
- Proactive Communication and Transparency: Ensuring open communication from the moment the order is received and long after the product is delivered can enhance the customer experience. Provide proactive communication, updating customers on order statuses and addressing potential delays sooner rather than later.
- Efficient Handling of Returns and Warranty Claims: Since returns are always a possibility, whether it’s due to dissatisfaction, damaged items, or errors in ordering, it’s crucial to streamline returns or warranty claims to retain customer loyalty, for example by providing automated return labels and flow sheets. A positive return experience can convert a one-time buyer into a lifelong advocate.
Auto Fulfillment Warehousing in the USA with Lean Supply Solutions
For seamless auto fulfillment, rely on the experts at Lean Supply Solutions. With access to multiple warehouses and optimized shipping routes, you can help your customers save money, thereby increasing your sales profits. We offer comprehensive, 24/7 support with integrated logistics solutions using lean processes and cutting-edge IT systems. Contact us today to discuss how our fulfillment solutions can enhance your automotive business!
- Published in Blog