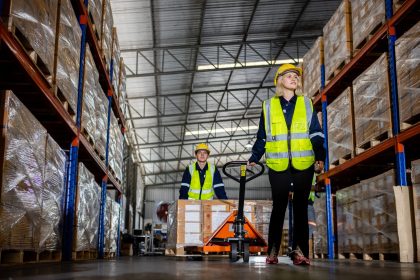
Inventory shrinkage, the loss of inventory that is unaccounted for, is a silent but significant threat to businesses, especially for those in the retail sector. It encompasses issues like theft, spoilage, administrative errors, and more. The cost can be staggering, both in terms of direct financial losses and the erosion of customer trust. However, with the right strategic approach, businesses can significantly reduce this risk.
This blog post is your comprehensive guide to understanding inventory shrinkage and what your business can do to prevent it.
Understanding Inventory Shrinkage
Inventory shrinkage is a compound issue, made up of many moving parts. The reality is that every business that sells a product can expect to see some amount of shrinkage. According to reports released by Deloitte Canada studies, retail shrinkage costs global markets nearly $95 billion each year.
The key is to reduce the risk of inventory shrinkage in areas where it can be prevented. For every item recorded as shrinkage, it must be documented as an expense (money lost).
Calculate your inventory shrinkage rate with this formula:
Inventory Shrinkage Rate = (Recorded Inventory – Actual Inventory) / Recorded Inventory
Inventory shrinkage can occur due to both internal and external factors. These aspects can be intentional or unintentional. Below are some of the main causes of inventory shrinkage:
- Theft: With nearly three-quarters of shrinkage attributed to internal/external theft, inventory control is essential. Brick-and-mortar stores can see an increase in inventory shrinkage due to shoplifting, employee theft, and fraud by suppliers.
- Administrative Errors: Inventory shrinkage can be unintentional due to administrative errors. Miscounts, damaged products not being removed from inventory, and similar errors can lead to inaccuracies in stock levels.
- Damage: Whether products are received by the company or customer with visible damage, it is considered a loss. Inventory shrinkage can increase if goods have cracks, water damage, or tears.
- Spoilage: With all good intentions, food and beverage products can succumb to spoilage. This increases the amount of inventory shrinkage.
- Vendor Fraud: It may seem improbable, but inventory shrinkage can be linked to fraudulent vendors. A dishonest vendor might exaggerate the amounts of goods delivered or their quality.
- Miscounts: Large stocks of inventory can be prone to miscounts through human error during physical or cycle counts. These mistakes can cause inaccurate record keeping, leading to overstocks or stockouts.
- Return Fraud: This cause of inventory shrinkage is directly linked to customers returning stolen products and receiving refunds through means of fraud.
The Consequences of Inventory Shrinkage
Inventory shrinkage can impact retailers in various ways. This is why inventory shrinkage prevention is essential for maintaining good business operations. Below are some of the consequences of inventory shrinkage.
- Financial implications: Loss of revenue and decreased profitability are significant penalties due to inventory shrinkage. Basically, for every product wasted, money is lost. Financial implications can also be experienced when there are accounting miscalculations.
- Operational disruptions: Inventory shrinkage can result in order delays, stockouts, and discrepancies, all of which can interfere with the day-to-day operations of the business.
- Reputational damage: If measures are not taken to reduce inventory shrinkage, customer loyalty and trust can decrease. Problems with order processing, fulfillment, and delivery can cause customers to seek business elsewhere.
Strategies to Prevent Inventory Shrinkage
Now that we’ve established the significance of preventing inventory shrinkage, it’s time to explore some proactive strategies to safeguard your stock. While some inventory shrinkage cases are inevitable, most can be prevented with strategic management systems.
Implement Robust Inventory Management Systems
An effective system for managing your inventory is a crucial first step in preventing shrinkage. It is essential to have clear guidelines and processes for all inventory-related activities, from receiving to shipping. This clarity ensures that there are no ambiguities that could lead to shrinkage.
Utilize barcode scanning and inventory management software to increase the accuracy and efficiency of inventory tracking. These tools can vastly improve the speed and precision of your inventory management processes.
Enhance Security Measures
As many causes of inventory shrinkage are associated with theft, installing security measures at every corner of the supply chain is worth the investment. From surveillance cameras, alarm systems, access control, and two-signature processing, inventory theft can be prevented.
Limiting access to storage areas can greatly reduce the opportunity for theft. Only authorized personnel should be able to enter these spaces. In addition, visible security measures can act as deterrents for potential thieves. In the event of an incident, alarms can alert staff to the problem, enabling a swift response.
Regular Inventory Audits
Inventory cycle counts and regular audits can be time-consuming but can save thousands of dollars if an error in the inventory is found. Instead of waiting for an annual inventory count, the cycle counting method allows for regular checks on different sections of your inventory without halting operations.
Implementing real-time inventory technology can also be helpful to reduce shrinkage issues without causing operational delays or shutdowns. Scheduled and surprise audits are recommended when internal theft is suspected.
Supplier and Vendor Collaboration
Building strong alliances with your suppliers and vendors is a smart approach for curbing shrinkage. Maintain open lines of communication and fair dealings to build trust and ensure suppliers are invested in your success.
Inventory shrinkage can happen at any level. Keep a watchful eye on vendor delivery times and the accuracy of invoices and quantities delivered. Hold vendors accountable for any discrepancies that could contribute to shrinkage.
Work with a Fulfillment Partner
Outsourcing your inventory and fulfillment services to a specialized provider can offer multiple advantages in preventing shrinkage. Third-party logistics providers often have sophisticated systems to handle inventory efficiently, reducing the risk of shrinkage.
By outsourcing fulfillment services, a business can ensure its inventory management is secure and benefit from smoother receiving, storage, and order fulfillment processes. Professionally managed warehouses are better equipped to handle inventory securely, minimizing damage and theft.
Contact Lean Supply Solutions for Customized Inventory Management Solutions
Inventory shrinkage is a complex challenge, but it is not insurmountable. Implementing the strategies outlined in this guide will help you minimize the risk and impact of inventory shrinkage. For businesses looking to go beyond the basics, partner with Lean Supply Solutions. We offer superior fulfillment services based on our Lean Methodology principles.
Contact us today to discuss how we can help lower your inventory shrinkage with our customized inventory management solutions.